
/
/
Apartment building in Bezannes, 2025
The ViliaSprint² project marks France’s first locally printed building
and another impressive first: 100% load transfer through the 3D-printed walls.
A multi-family building with 12 social housing units on three floors is currently being built in Champagne, France, and is being 3D printed on-site for the first time. The project combines numerous aspects of modern, sustainable housing: bio- and geo-based materials, a central heat pump, and a photovoltaic system. All loads are transferred directly into the 3D-printed structures – a major milestone for 3D building printing.
Location
Project category
Residential construction
Pure printing time
Will be printed until June 2025
Project participants
Plurial Novilia
Demathieu Bard Architecture Office HOBO
Holcim Lafarge
Engineering office Socotec
Amodis Engineering Office
IMPRESSIONS OF THE PROJECT IMPLEMENTATION
Big building. Big goals.

Hello France!
ViliaSprint² marks our first 3D printing project in France and the country's first in-situ printed building. Measuring 11 meters wide, 34 meters long, and 9 meters high, each floor offers 350 m² of usable space. This makes the project the largest 3D-printed apartment building in Europe. The building had to be relocated several times for implementation.
Strong material. Strong statics.
A 3D-printed concrete from Holcim Lafarge is used, which offers very high structural strength and improved fire protection properties. 100% of the loads are transferred through the walls printed from this material. Thus, the project delivers, for the first time, fully load-bearing 3D-printed wall structures.
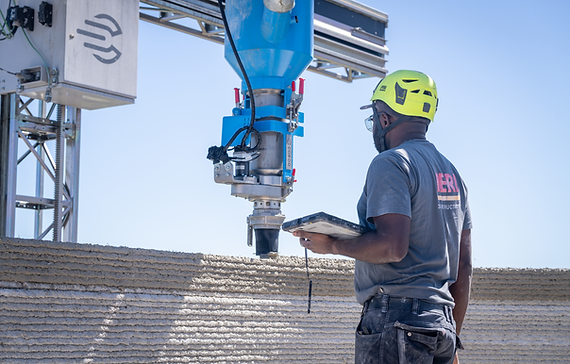

3D printing or conventional?
ViliaSprint ² consists not only of a 3D-printed apartment building, but also of a second, conventionally constructed building directly next door. The two structures are being built simultaneously to allow comparisons both during construction and later during operation.
Impressions from the construction site
Here you can find more impressions from the 3D printing construction site in France.
The project at a glance
The video gives you even more insight into what's going on at the 3D printing construction site in Bezannes. Check it out!
Requirements and solutions
Requirements
The printing phase is estimated to take less than three months – one floor will be printed in approximately four weeks. Compared to conventional construction methods, this should reduce the construction time for the supporting structure by two months. The size of the building also exceeds the printing capacity of the COBOD BOD2, so a solution had to be found.
Solutions
For implementation, the building was divided into two segments, between which the printer was moved several times during the construction process. This allows for significant time savings, as the ceilings can be built in the non-actively printed segment. This ensures optimal printer utilization and optimizes the construction process. The load transfer provided by the 3D-printed structures also saves a considerable amount of building material.
Customer benefit
ViliaSprint ² is currently under construction, but the project's significance for both Bezannes and the 3D printing technology is enormous. By transferring loads, the construction will mark an important milestone, while providing affordable housing for the village's residents. Furthermore, the direct comparison between the printed and conventionally constructed residential building will provide many insights that the industry can build upon together.
HERE EVERYTHING INTERLOCKS
Products in use
IF YOU ARE NEARBY